Service Report – 20 Moving Heads
Introduction
For this project we were contacted by our client who had 20 Chauvet 375z moving heads installed around an ice rink. The environment at an ice rink is quite harsh for equipment due to humidity and low temperature, as well as access issues above ice making regular cleaning difficult. Because of these conditions, the venue had been keeping the lights on 24/7 for the last 3 years. The lights had not been serviced in this time.
When some of the LEDs started to turn blue while set to white, we were called in to assess the situation. We started with a site survey and visual inspection which included tagging each light with a unit number and the DMX address it had been assigned at installation. We made notes about any faults that were present at this point. We then carefully removed the fixtures and boxed them up, which we then transported back to our workshop for a thorough analysis. Below you can see a video of 10 of the lights on our workbench before we started work.
Service Report
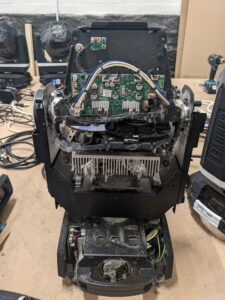
Before
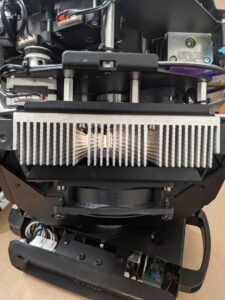
After
In the images to the left, you can see a before and after of the inside of the lights. As you can see, they were in really poor condition and required some extensive cleaning to bring back to their former glory. Not only were the air inlets blocked, but the insides were covered in a thick layer of dust. The colour wheels were dirty which would effect the output level of the light and would project dust patterns onto surfaces.
We set up each light in turn and ran a full diagnostic. This included a factory reset and testing of all their features such as gobo wheels, colour wheels, and prisms. As you can see from the photos, these lights were extremely dusty inside and out. The air inlets and fans were worst affected which causes issues with cooling and will shorten the life of LED lights. Written notes were made of any additional faults on the lights. Once the lights were fully assessed, we set to work giving them a full clean. We removed the outer enclosures of the fixtures and then used compressed air to blow out all the loose dust. We then cleaned each part using anti static cleaner and microfibre clothes. In total, 9 of the fixtures had faults which included the previously mentioned colour issue with the LED, and a couple fixtures had motors that were failing.
The faulty lights were set aside, and the fully functional lights were reassembled. We then ran a PAT test on them and made a record of this.
The lights which had turned blue required new LEDs which we placed on order with Chauvet for later replacement. We also ordered new tilt motors for 2 fixtures.
Due to the current situation with supplies, we would have to wait a few weeks for the parts delivery to come in. As the venue would require lighting during this time, we made the decision to reinstall the known good lights in the mean time.
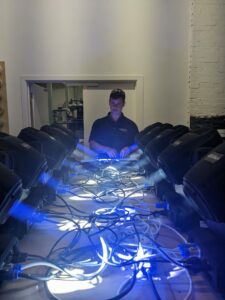
Intelligent lights being tested by our staff
Conclusion
Regular servicing of AV and other electrical equipment is very important in order to maintain safety and to prolong the life of the fixture. LEDs will typically have a life span of 50,000 hours, however this is shortened considerably in harsh environments, particularly when hot. In this case they had been running non-stop for over 3 years and the fans and air inlets were blocked with dust, meaning they are starting to come to the end of their life. We advised the client that the other fixtures may require work in the coming year or so. We set up a service plan with the client which includes regular inspections and yearly PAT testing. LSL have a dedicated service department maintaining our fleet of rental equipment and servicing 3rd party equipment. If you have any fixtures that require service, please get in touch to find out how we can help.
So, which issues have you experienced with your AV gear? Let us know down in the comments.